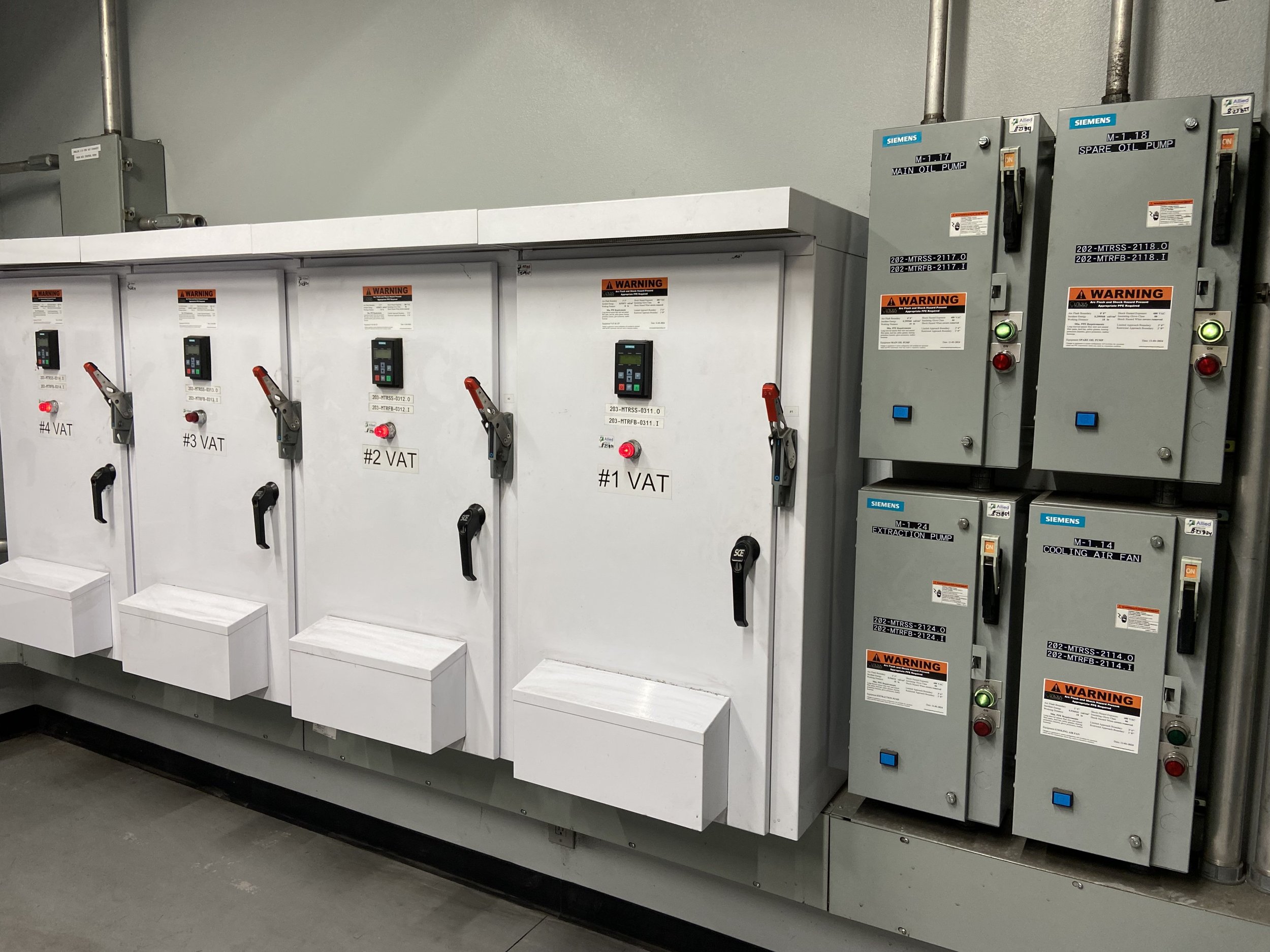
case studies
case 1
saving money & enhancing safety
-
A large manufacturing facility, over 50 years old, operates with outdated equipment and no electrical documentation. Over the years, expansions and modifications have left the system undocumented, raising red flags for the fire department and insurance provider. At the same time, management is concerned about worker safety, OSHA compliance, and liability risks.
-
We would step in to transform this challenge into an opportunity by:
Creating a One-Line Diagram: The facility’s first comprehensive electrical system map to serve as a foundation for safety assessments and future upgrades.
Identifying and Mitigating Hazards: Pinpointing high-risk areas and recommending updates to grounding, protective devices, and work practices.
Ensuring Compliance: Providing clear PPE guidelines, arc flash boundaries, and equipment signage in alignment with OSHA and NFPA 70E.
Satisfying Stakeholders: Addressing fire department and insurance concerns through proactive documentation and safety enhancements.
-
OSHA compliance and reduced liability.
Simplified maintenance and troubleshooting with the new one-line diagram.
Mitigated electrical risks and fewer incidents.
Lower insurance premiums due to improved safety.
-
Older facilities face unique challenges, but with the right expertise, safety and efficiency can be dramatically improved. Curious Engineering Consulting delivers tailored solutions that turn concerns into opportunities for long-term success.
Client: A Dated, Industrial Manufacturing Facility
Services: Arc Flash Assessment, Short-circuit Assessment & Device Evaluation
case 2
transforming operations
-
A family-owned brewery struggles to keep up with growing demand due to a slow, labor-intensive manual bottling line. Rising labor costs and limited resources make it hard to meet production goals. With a tight budget ruling out full automation, the brewery risks losing customers if they can’t increase efficiency.
-
We would design a cost-effective, semi-automated bottling solution to boost production while staying within budget by:
Custom Control Panel Design: Tailored to the brewery’s needs, using trusted brands and UL 508A standards.
Automating Key Processes: Focusing on repetitive tasks like filling and capping to save time, while keeping less critical tasks manual.
User-Friendly Interface: A simple control system for operators to easily monitor and manage the line.
Scalable Design: Meeting current production needs with room to upgrade as the brewery grows.
-
30% More Production: Meets and exceeds daily bottling targets.
Lower Labor Costs: Frees up employees for other tasks.
Improved Quality: Reduces errors and waste for consistent product quality.
Rapid ROI: An affordable solution with room for future expansion.
-
Automation doesn’t have to break the bank. A semi-automated solution bridges the gap for small businesses, improving efficiency and meeting growing demand while staying budget-friendly. Curious Engineering Consulting specializes in crafting scalable, practical solutions that empower small businesses to thrive.
Client: A Small Brewery
Services: Control Panel Fabrication & Automation
case 3
reducing downtime
-
A food processing plant faces frequent breaker trips that disrupt production and lead to costly unplanned downtime. Each incident halts operations, resulting in financial losses and missed deadlines. The culprit? Improper coordination between protective devices causes multiple breakers to trip simultaneously, unnecessarily shutting down large sections of the plant.
-
We would perform a coordination study to streamline the plant's electrical system by:
Analyzing Protective Devices: Identifying coordination issues through detailed time-current characteristic analysis.
Adjusting Device Settings: Fine-tuning breaker settings to ensure only the device closest to the fault trips, keeping the rest of the system running.
Minimizing Disruption: Collaborating with the maintenance team to implement changes with minimal impact on production.
Providing Documentation: Delivering a report with implemented changes and recommendations for future reliability.
-
20% Less Downtime: Over six months, downtime is significantly reduced, boosting efficiency.
Enhanced System Reliability: Proper coordination isolates faults without shutting down the entire system.
Increased Productivity: Fewer interruptions allow the plant to consistently meet production goals.
Proactive Maintenance Insights: Detailed analysis supports better planning for future upgrades.
-
Coordination studies ensure protective devices work seamlessly, minimizing disruptions and maximizing efficiency. At Curious Engineering Consulting, we help facilities like this food processing plant reduce costs and keep operations running smoothly, ensuring production targets are met and profits are protected.
Client: A Food Processing Facility
Services: Coordination Study
case 4
reduce costs with Sustainable energy
Client: A Commercial Property Owner
Services: Electrical Design & Project Management
-
A commercial property owner needs to upgrade their electrical utility service to support new equipment and integrate solar panels to reduce energy costs and boost sustainability. However, the project is complex: obtaining permits requires detailed, stamped drawings, navigating utility requirements is daunting, and managing the upgrade is outside the client’s expertise.
-
We would provide a tailored, end-to-end solution, including seamless solar panel integration, by:
Electrical Design and Drawings:
Preparing precise, code-compliant drawings, including one-line diagrams, load calculations, and solar system schematics.
Providing stamped documents ready for AHJ and utility company approvals.
Solar Panel Integration:
Designing the system to integrate seamlessly with the upgraded utility service, ensuring compliance with interconnection standards.
Maximizing energy efficiency to align with sustainability goals and reduce costs.
Stakeholder Coordination:
Streamlining the permitting process by liaising directly with the AHJ, utility company, and solar providers.
Project Management:
Overseeing the project from design through installation, coordinating contractors, ensuring compliance, and addressing any challenges.
-
Quick Approvals: Permits for the utility upgrade and solar installation are secured without delays.
Efficient Installation: The upgraded electrical service and solar system are installed seamlessly and meet all regulations.
Expanded Capacity: The new system supports increased energy demands while reducing energy costs through solar power.
Sustainability Achieved: Solar integration lowers the carbon footprint and may qualify for renewable energy incentives.
-
At Curious Engineering Consulting, we specialize in simplifying complex projects like utility upgrades and green energy integration. By providing expert designs and project coordination/management, we help commercial property owners meet energy demands, achieve sustainability, and stay ahead in a renewable energy future.
case 5
elevating safety & regulatory compliance
-
A manufacturing facility narrowly avoids a serious incident when a maintenance worker attempts to troubleshoot a live machine without proper training. The event exposes gaps in safety protocols, leaving the team at risk for future accidents and non-compliance with OSHA regulations.
-
We would deliver a hands-on training program tailored to the facility's specific needs, equipping workers with the skills to safely manage electrical tasks while ensuring compliance.
Customized Training Program:
Electricity 101: Build foundational knowledge of electricity and the operation of control and protective devices.
Codes and Regulations: Review key standards, including NFPA 70E, OSHA 1910 Subpart S, and NEC, for full compliance.
Electrical Hazards: Train workers to recognize and prevent risks like shock and arc flash.
Safe Work Practices: Teach critical safety procedures like lockout/tagout (LOTO).
Basic Troubleshooting: Provide hands-on instruction for troubleshooting techniques, including safe multimeter use.
Engaging Learning Tools:
Detailed workbooks and quizzes for active learning.
Extensive hands-on training to reinforce practical skills.
-
Improved Safety: Workers are prepared to safely handle electrical tasks, reducing incidents.
Regulatory Compliance: Training aligns the facility with OSHA and NFPA 70E requirements.
Enhanced Confidence: Employees gain the skills to recognize hazards and act proactively.
Safety Leadership: By addressing safety concerns head-on, the facility demonstrates its commitment to protecting workers and operational excellence.
-
Curious Engineering Consulting empowers teams to prioritize safety and meet regulatory standards. Whether resolving an issue or taking proactive steps, our training delivers lasting value—protecting workers and fostering a culture of safety and compliance.
Client: An Industrial Manufacturing Facility
Services: Qualified Electrical Worker Training